OUR GREEN POLICY
ENVIRONMENTAL FOCUS
As an environmentally concerned organization we have made substantial contribution in this regard.
- We use azo-free dyes and chemicals in our dyeing house which are also complying with Reach and Oekotex standards
- 15% of our energy consumption is met through Wind energy, produced by our parent concern s p spinning mills pvt ltd., which is a fully wind powered facility.
- Only 50 to 55 Ltrs of water per Kg of yarn is used as against the industrial norms of 85 to 90 Ltrs of water per Kg of yarn, through selection of lower MLR machines and process control and optimisation of process sequences.
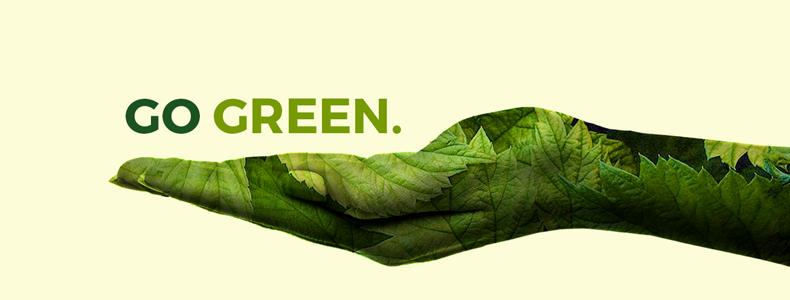
- We have implemented condensate recovery system in 2003, where water and heat energy are recovered and re-used by the boiler.
- We have rain water harvesting facility of total catchment area of 6576 cu. Mtrs and at present we are harvesting about 70% of the potential and use it to recharge ground water with rain water.
- Ours is a ‘Zero Liquid Discharge’ (ZLD) facility since March 2006, which means no liquid from the process is discharged to environment.
- Only 2% of our process water is lost due to evaporation (98% is recycled). Currently studies are underway to reduce this loss further.
- Benefits of water and salt recycling include,
- Elimination of pollution load to environment
- Substantial reduction in depletion of fresh water and salt sources
- Reduction in carbon footprint of water and salt supply vehicles
- Minimal process dependence on the availability of fresh water and salt.
OUR QUALITY POLICY
We at, s p textile processors pvt ltd, shall continuously strive to improve and provide quality service to meet the multi various needs of the textile industry. This service shall be aimed at enhancing satisfaction of our customers and thus becoming their “NATURAL CHOICE”.
OUR ENVIRONMENTAL POLICY
We at s p textile processors pvt ltd, aim to continuously improve our environmental performance, considering the impact of our processes on the environment and move towards being an ‘ECO-FRIENDLY’ Organization.
We will,
- comply with the applicable legal, statutory and other environmental requirements, reduce our specific fresh water consumption, thermal and electrical energy consumption,
- prevent or minimize pollution at source,
- adopt innovative techniques and technology to increase the percentage of water recovered from our effluents and
- train our employees in the best practices for efficient use of water and electrical energy.
Currently, We have installed state-of-art machineries supplied by the pioneers in the corresponding segments like Dalal, Fongs, SMEW-Filcano, Tecnorama & for ETP like Koch, Hyflux, GE Osmonics, Codeline & Grundfos.
OUR WATER AND SALT RECYCLING PLANT
We have implemented condensate recovery system in 2003, where water and heat energy are recovered and re-used by the boiler.
OTHER ENVIRONMENTAL FACTS
As an environmentally concerned organization we have made substantial contribution in this regard.
Benefits of water and salt recycling include,
- Elimination of pollution load to environment.
- Substantial reduction in depletion of fresh water and salt sources.
- Reduction in carbon footprint of water and salt supply vehicles.
- Minimal process dependence on the availability of fresh water and salt.